隨著我國環(huán)境壓力逐年增大,國家排放要求進(jìn)一步收緊,電廠煙氣脫硫技術(shù)也得到了快速發(fā)展。目前煙氣脫硫技術(shù)種類達(dá)幾十種,按脫硫過程是否加水和脫硫產(chǎn)物的干濕形態(tài),煙氣脫硫分為:濕法、半干法、干法三大類脫硫工藝。
目前,濕法煙氣脫硫技術(shù)最為成熟,已得到大規(guī)模工業(yè)化應(yīng)用,但由于投資成本高還需對工藝和設(shè)備進(jìn)行優(yōu)化;干法煙氣脫硫技術(shù)不存在腐蝕和結(jié)露等問題,但脫硫率遠(yuǎn)低于濕法脫硫技術(shù),一般單想電廠都不會選用,須進(jìn)一步開發(fā)基于新脫硫原理的干法脫硫工藝;半干法煙氣脫硫技術(shù)脫硫率高,但不適合大容量燃燒設(shè)備。不同的工況選擇最符合的脫硫方法才會得到最大的經(jīng)濟(jì)效益。揭下來根據(jù)電廠脫硫技術(shù)的選擇原則來分析各種工藝的優(yōu)缺點(diǎn)、適用條件。
電廠脫硫技術(shù)的選擇原則:
1、脫硫技術(shù)相對成熟,脫硫效率高,能達(dá)到環(huán)??刂埔?,已經(jīng)得到推廣與應(yīng)用。
2、脫硫成本比較經(jīng)濟(jì)合理,包括前期投資和后期運(yùn)營。
3、脫硫所產(chǎn)生的副產(chǎn)品是否好處理,最好不造成二次污染,或者具有可回收利用價值。
4、對發(fā)電燃煤煤質(zhì)不受影響,及對硫含量適用范圍廣。
5、脫硫劑的能夠長期的供應(yīng),且價格要低廉
濕法煙氣脫硫技術(shù)
濕法煙氣脫硫技術(shù)是指吸收劑為液體或漿液的脫硫技術(shù),最大的優(yōu)點(diǎn)是反應(yīng)速度快、脫硫效率高,最大的缺點(diǎn)就是前期投資、后期運(yùn)行成本高和副產(chǎn)品處理困難。濕法煙氣脫硫技術(shù)是目前技術(shù)最為成熟,也是我國使用最廣泛的,據(jù)不完全統(tǒng)計, 已建和在建火電廠的煙氣脫硫項(xiàng)目中, 90 % 以上采用濕法煙氣脫硫技術(shù)。
1石灰石—石膏濕法脫硫工藝
工藝流程
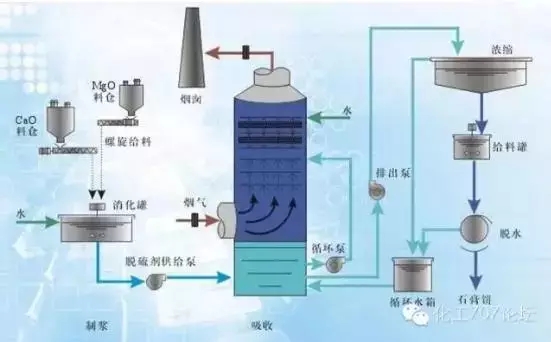
石灰石—石膏濕法脫硫技術(shù)是將石灰石粉加水制成漿液作為吸收劑泵入吸收塔與煙氣充分接觸混合,煙氣中的二氧化硫與漿液中的碳酸鈣以及從塔下部鼓入的空氣進(jìn)行氧化反應(yīng)生成硫酸鈣,硫酸鈣達(dá)到一定飽和度后,結(jié)晶形成二水石膏。經(jīng)吸收塔排出的石膏漿液經(jīng)濃縮、脫水,使其含水量小于10%,然后用輸送機(jī)送至石膏貯倉堆放,脫硫后的煙氣經(jīng)過除霧器除去霧滴,再經(jīng)過換熱器加熱升溫后,由煙囪排入大氣。由于吸收塔內(nèi)吸收劑漿液通過循環(huán)泵反復(fù)循環(huán)與煙氣接觸,吸收劑利用率很高,鈣硫比較低,脫硫效率可大于95% 。
技術(shù)和經(jīng)濟(jì)性
石灰石—石膏法脫硫工藝流程簡單、技術(shù)先進(jìn)又可靠,脫硫效率高達(dá)95%以上,是目前國內(nèi)外煙氣脫硫應(yīng)用最廣泛的脫硫工藝。但是系統(tǒng)復(fù)雜、設(shè)備龐大、耗水量大、一次性投資高,一般適用于大型電廠。
催化劑及副產(chǎn)品處理與利用
使用的催化劑為石灰石,資源豐富,價廉易得。生成物是液體或淤渣,較難處理,經(jīng)濃縮、脫水后可用來制石膏,但是對設(shè)備腐蝕性嚴(yán)重,結(jié)垢堵塞問題不易解決。
適用范圍
單塔處理脫硫量大,適用于任何含硫量的煤種的煙氣脫硫,對鍋爐的適應(yīng)性強(qiáng),一般在大型電廠或大功率鍋爐使用。
2雙堿脫硫工藝
工藝流程
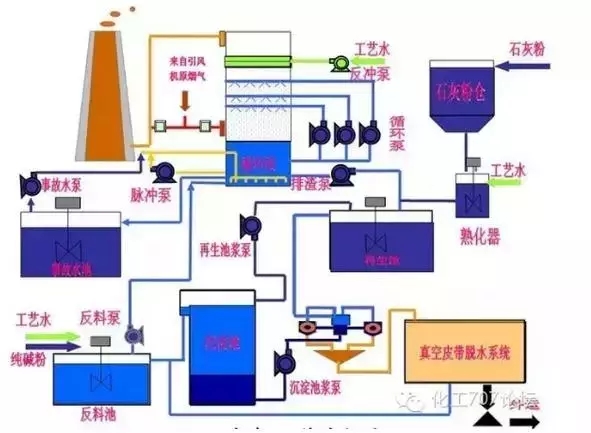
雙堿法煙氣脫硫技術(shù)是利用氫氧化鈉溶液作為啟動脫硫劑,配制好的氫氧化鈉溶液直接打入脫硫塔洗滌脫除煙氣中?SO2?來達(dá)到煙氣脫硫的目的,然后脫硫產(chǎn)物經(jīng)脫硫劑再生池還原成氫氧化鈉再打回脫硫塔內(nèi)循環(huán)使用。
技術(shù)和經(jīng)濟(jì)性
雙堿法煙氣脫硫技術(shù)是為了克服石灰石—石灰法容易結(jié)垢的缺點(diǎn)而發(fā)展起來的。技術(shù)相對比較成熟,小型鍋爐、窯爐脫硫除塵絕大多采用雙堿法脫硫 除塵工藝。在前期投資較省,但長期運(yùn)營成本高。
催化劑及副產(chǎn)品處理與利用
雙堿法是采用鈉基脫硫劑進(jìn)行塔內(nèi)脫硫,以氫氧化鈉為原料,脫硫系統(tǒng)的最終脫硫產(chǎn)物仍然是石膏漿,具體成分為 CaSO3 、 CaSO4 ,還有部分被氧化后的鈉鹽 NaSO4 。從沉淀池底部排漿管排出,由排漿泵送入水力旋流器。由于固體產(chǎn)物中摻雜有各種灰分及 NaSO4 ,嚴(yán)重影響了石膏品質(zhì),所以一般以拋棄為主。
適用范圍
雙堿法脫硫工藝降低了投資及運(yùn)行費(fèi)用,比較適用于中小型鍋爐進(jìn)行脫硫改造的脫硫除塵器。
3氨法煙氣脫硫工藝
工藝流程
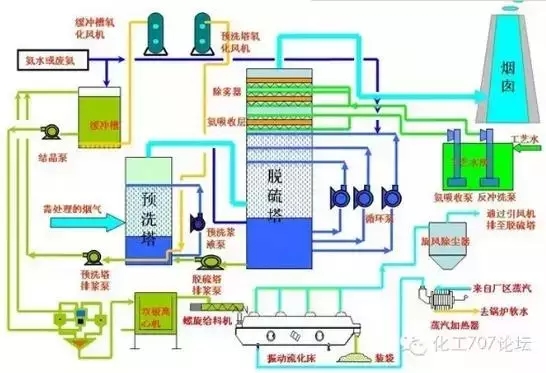
含二氧化硫煙氣通過鍋爐引風(fēng)機(jī)進(jìn)入預(yù)洗塔的底部,與洗滌水逆流接觸,清出煙氣中的灰塵,然后煙氣經(jīng)均布器升入濃縮段利用煙氣熱量提濃脫硫液,煙氣溫度降至50℃~60℃,再進(jìn)入脫硫塔吸收段。在吸收段,煙氣與氨水液充分接觸反應(yīng),吸收掉絕大部分的SO2,最后經(jīng)除霧器除霧成為凈化煙氣,通過脫硫塔頂部煙囪排放。液相吸收劑氨水經(jīng)氨水泵送入脫硫塔,吸收煙氣中的SO2生成亞硫酸銨,生成物在脫硫塔底部(有的在塔外氧化)氧化段被空壓機(jī)鼓入的空氣氧化成硫酸銨溶液。部分硫酸銨溶液打入洗滌濃縮段,一方面煙氣冷卻,同時自身水分得到蒸發(fā),形成固含量約為5%~10%的硫酸銨漿液。
技術(shù)和經(jīng)濟(jì)性
氨法脫硫工藝雖然起步晚,但也已經(jīng)成熟。相對于石灰石-石膏法脫硫工藝來說,氨法脫硫可較容易實(shí)現(xiàn)98%以上的脫硫效率,并可與SCR等脫硝工藝共用氨供應(yīng)系統(tǒng)等,且副產(chǎn)品硫酸銨利用價值相對較高,經(jīng)濟(jì)效益明顯,逸氨量控制技術(shù)需要完善,否則氮氧化物會破壞大氣。美國John Brown工程師和建筑師有限公司表示:通過大量、高價值的副產(chǎn)品生產(chǎn),氨法煙氣脫硫可以獲得卓越的投資效益。
催化劑及副產(chǎn)品處理與利用
氨法以氨為原料,其形式可以是液氨、氨水和碳銨。目前我國火電廠年排放二氧化硫約1000萬噸,即使全部采用氨法脫硫,用氨量不超過500萬噸/年,供應(yīng)完全有保證。
氨回收法脫硫裝置的運(yùn)行過程即是硫酸銨的生產(chǎn)過程,每吸收1噸液氨可脫除2噸二氧化硫,生產(chǎn)4噸硫酸銨。
適用范圍
處理脫硫量大,適用范圍廣,設(shè)備較簡單,即可滿足大型電廠的使用要求,也更容易實(shí)現(xiàn)舊鍋爐的改造,可大幅提高脫硝效率。
4氧化鎂法脫硫工藝
工藝流程
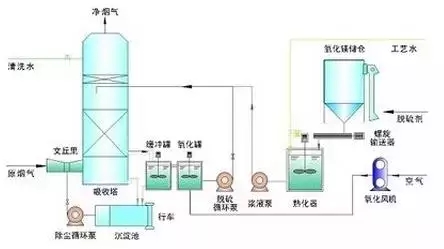
鍋爐煙氣由引風(fēng)機(jī)送入吸收塔預(yù)冷段,冷卻至適合的溫度后進(jìn)入吸收塔,往上與逆向流下的吸收漿液反應(yīng),氧化鎂法脫硫法脫去煙氣中的硫份。吸收塔頂部安裝有除霧器,用以除去凈煙氣中攜帶的細(xì)小霧滴。凈煙氣經(jīng)過除霧器降低煙氣中的水分后排入煙囪。粉塵與臟東西附著在除霧器上,會導(dǎo)致除霧器堵塞、系統(tǒng)壓損增大,需由除霧器沖洗水泵提供工業(yè)水對除霧器進(jìn)行噴霧清洗。
技術(shù)和經(jīng)濟(jì)性
有資料顯示,目前美國、歐洲、日本火電廠80%的機(jī)組容量均采用鎂法脫硫,中國臺灣電廠的95%機(jī)組容量也是采用鎂法脫硫技術(shù)相對成熟。由于氧化鎂作為脫硫本身有其獨(dú)特的優(yōu)越性,因此在吸收塔的結(jié)構(gòu)設(shè)計、循環(huán)漿液量的大小、系統(tǒng)的整體規(guī)模、設(shè)備的功率都可以相應(yīng)較小,這樣一來,整個脫硫系統(tǒng)的投資費(fèi)用可以降低20%以上,不易結(jié)垢,設(shè)備維護(hù)方便。
催化劑及副產(chǎn)品處理與利用
氧化鎂法脫硫法以氧化鎂為原料,在我國氧化鎂的儲量十分可觀,目前已探明的氧化鎂儲藏量約為160億噸,占全世界的80%左右。脫硫系統(tǒng)的最終脫硫產(chǎn)物主要是硫酸鎂溶液,硫酸鎂溶液通過泵輸送至硫酸鎂后處理工段,進(jìn)行蒸發(fā)結(jié)晶、離心脫水及干燥包裝等處理,制備出七水硫酸鎂。
適用范圍
氧化鎂法脫硫法適用性強(qiáng),大小規(guī)模的鍋爐均可滿足。
目前我國石灰石—石膏濕法脫硫工藝在電廠脫硫方面一家獨(dú)大,但是在成本、運(yùn)行穩(wěn)定性、反應(yīng)生成物處理方面有明顯劣勢,更加高效穩(wěn)定的氨法和氧化鎂法脫硫工藝會逐步推廣,蠶食石灰石—石膏濕法脫硫工藝的市場。